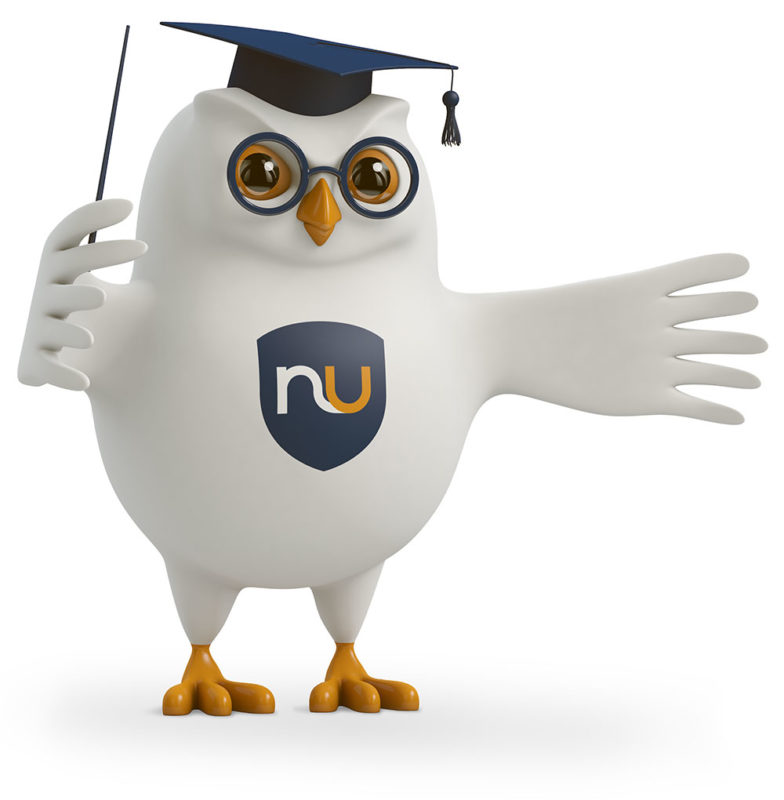
Hello! My name is Owlbert Einstein, the Print Finishing Expert at Nobelus. The Nobelus University is my library of knowledge about products, applications, markets, and special insights. Also, just for you, I offer a continually growing public FAQ’s center where you can find answers to many print related questions.
Don’t find the question you are trying to answer? Simply type in the question and I will get back to you in an email in the next 2-3 business days. Have a look around… What questions do you have about print?
Can’t find it? Submit your question to Nobelus University.
[fc id=’2′][/fc]
[ultimate-faq-search]
[ultimate-faqs]