FLEXIBLE PACKAGING AS A PROCESS
Flexible packaging has quickly become a mainstay in nearly every modern market and industry, gradually rising in popularity as more brands and consumers benefit from its affordability, versatility, and portability. Despite the proliferation of flexible packaging, the average person is likely unaware of how much careful planning and skillful execution go into creating even the simplest candy bar wrapper. Brands that utilize flexible packaging in their product lines may wonder why seemingly small changes, such as different materials or a slight tweak to the package’s shape, can have a significant effect on cost and performance. Given that flexible packaging is used daily by most everyone in today’s society, brands, consumers, and new flexpack converters alike can benefit from a quick overview of how it is produced and how many people play a role in getting these packages to the store shelves.
TURNING RAW MATERIALS INTO FILM WEB
Before we can discuss how packaging is assembled or given unique designs, it is important to understand that most flexible packaging is made from a variety of materials. A single flexible package typically consists of several distinct, incredibly thin layers, each of which is made of a different material that has been carefully selected to enhance the package’s overall structure. Many of these materials are used in other types of packaging, as well. However, for flexible packaging, they must be formed into a thin web so they can be layered together seamlessly.
PLASTIC
By far the most popular material type used in flexible packaging, plastic films are created by first refining crude oil, natural gas, and sometimes coal into petroleum. From petroleum, monomers such as ethylene and propylene can be produced. These monomers are combined into long chains to create polymers, which serve as basic building blocks that can be formed into a variety of shapes. To create the thin film web used in flexible packaging, these polymers are melted down and then pressed through a very thin slot in a process called blown film extrusion. The resulting web holds together very well unless a significant amount of force is applied, making it ideal for lightweight flexible packaging.
A variety of plastics are used in flexible packaging, and each has its own unique properties that make it suitable for specific applications. Polyester (PET) and nylon are frequently used to prevent a package from being punctured or torn, while polypropylene (OPP) is often used for a heat-sealable layer. Ethylene vinyl acetate (EVA) is a type of plastic that is frequently used as an adhesive.
PAPER
While paper web used in the production of flexible packaging differs from paper used for writing, it is still manufactured in a similar method. Wood from trees is shredded and boiled to produce pulp, which is then combined with various chemicals and dyes to achieve a precise mixture with specific qualities. A slurry consisting of liquid and tiny pulp fibers is squeezed out of the mixture over a mesh tray, leaving behind a flat layer of pulp that will become paper sheets once it is dried.
Ideal for environmentally conscious brands and converters, paper comes from a renewable resource, can typically be composted or recycled, and provides a way to reduce plastic usage in flexible packaging. However, the sustainability of paper in flexible packaging is dependent on the overall composition of the package as combining it with other materials may reduce or negate these benefits.
FOIL AND METALIZED FILM
Like other metal products, foil comes from unrefined ores that are mined from the earth. Once the ore, typically aluminum when referencing flexpack applications, is refined into its purest state, it is shaped into a thin web using a continuous mill. While aluminum foil is made entirely of metal, metalized films are actually plastic films with a metallic coating. In addition to simply layering aluminum over PET, metalized film can be created by superheating the metal in a vacuum until it evaporates and then flash cooling it so that it condenses on the surface of the film to create an incredibly thin layer of metal without damaging the plastic base film.
Metallic layers are often used to preserve the freshness and quality of products stored in flexible packaging by preventing the passage of gases and moisture. Their effectiveness in keeping out harmful substances makes foils and metalized films a requirement for barrier applications. They may also be used to give packaging a reflective finish for aesthetic purposes.
CONVERTING WEB INTO A PACKAGE
Once these various web materials have been manufactured, they are brought in-house by flexible packaging converters. Flexpack converters combine the individual web materials by layering them together and then shape them into the familiar packages seen on store shelves. While other industries may think of lamination as one of the last stages in the finishing process, flexpack converters use lamination throughout production as a way to combine each web layer with the next.
Converters may complete only one or two steps in the manufacturing process, or they may perform each step from sourcing to completion in-house. Converters with limited equipment capabilities may purchase pre-lams, or pre-laminated web, from other converters. Others may buy pre-made packaging that has already been laminated and shaped so they can focus on printing graphics on the package. Any converter who includes printing in their services is called a print converter. Let’s take a closer look at what happens within each step in the flexpack manufacturing process.
CREATING STRUCTURES
As mentioned previously, a single flexible package is typically constructed of several web layers. Each layer serves a vital purpose in protecting the stored product and ensuring the package meets the expectations of the brand. In an industry where one facility may produce millions of impressions a day, every penny counts. For this reason, material types, film thickness, adhesives, and the number of layers are all meticulously selected to account for price, performance, and equipment capabilities, resulting in a highly engineered structure with a deceptively simple appearance.
Anatomy of a Flexible Package
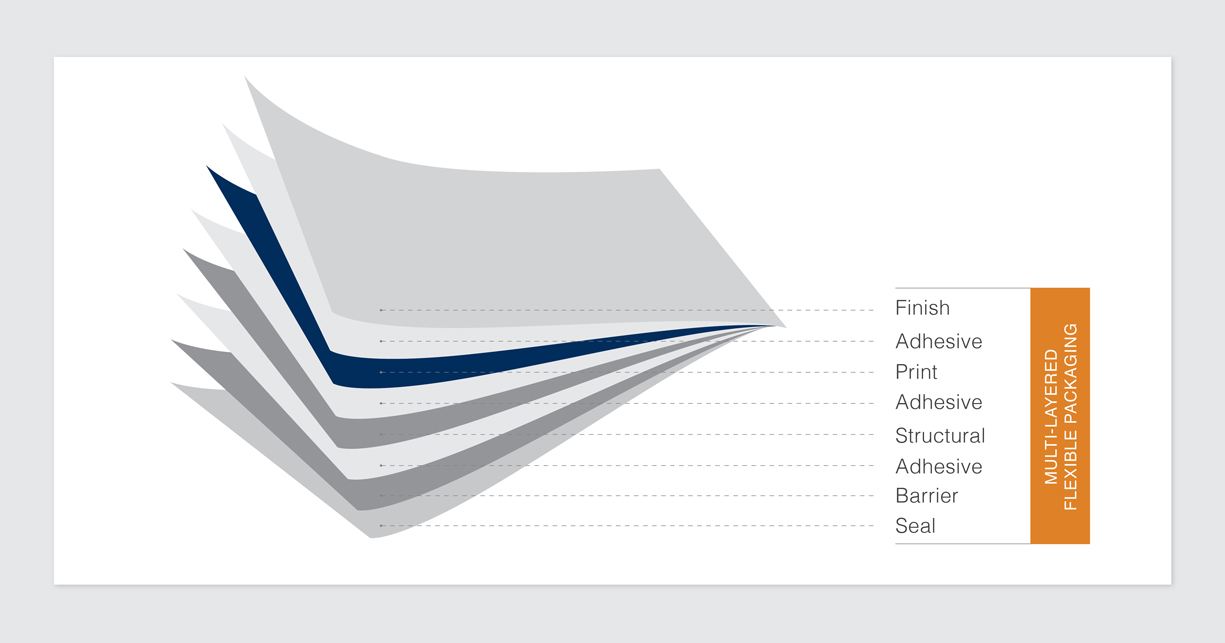
While the order, number, and type of layers used in flexible packaging can vary greatly, most packages follow a similar basic structure.
Seal Layer: As the innermost layer in the package, the seal layer typically needs to be made of a food-safe material that can be sealed together using heat.
Barrier Layers: The ultimate goal of a flexible package is to protect the product stored inside. For this reason, converters will usually include one or more barrier layers that prevent damage to the product. These barriers may block light, keep chemicals from seeping through, or prevent moisture or oxygen from penetrating the package.
Structural Layer: This layer exists chiefly to provide the package with a degree of rigidity. It is especially important in stand-up pouches, stick packs, and other applications that need to maintain a certain shape. Among all the layers in a flexible package, this one is the most optional.
Print Layers: The outermost layer on any flexible package, the print layers consist of whatever film receives ink and any finish that prevents the ink from smudging or scuffing off, such as such as an overlaminate or varnish. Converters who want to reduce costs while still burying the ink may choose to reverse print, which involves printing the design backwards on the inner side of a film so that it appears correct when the package is formed.
Not every flexible package uses several layers. Certain products require little in the way of protection, and in these instances, converters can minimize material costs by using a single film web, also known as a mono-material. This type of packaging is commonly used for fresh produce and highly processed bread.
Lamination Methods
Each layer in a flexible package is combined with the others using an adhesive, or tie layer. Several lamination methods are used in flexible packaging, each possessing its own strengths and weaknesses that can make it a better option for a given package.
Solventless, Solvent Based, and Water Based: These three lamination methods vary only in that they utilize adhesives with different carriers. They provide impressive bond strength for applications with high performance demands, but they may require multiple days to cure before they can be processed again. Among the three, solventless lamination is the most popular method due to its affordability and versatility.
Extrusion: Providing superior durability and puncture resistance, extrusion lamination is performed by feeding two web layers through a thin slot simultaneously. A molten resin is poured between the layers as they proceed through the gap, causing them to stick together when the resin quickly cools. Extrusion systems require a significant investment, but they can provide additional thickness for packaging without increasing the thickness of the film layers themselves.
Energy-Cured Systems: While energy-cured adhesives are used less frequently due to high equipment costs, they create a strong bond between layers and cure instantly as the adhesive is catalyzed using energy. This enables the laminated structure to be processed again immediately.
PRINTING AND FINISHING
After the web has been fully laminated and given all its functional layers, the outermost layer can receive a printed design. The pre-press and printing process varies greatly depending on which type of press the converter uses. Converters with conventional presses, such as a flexographic or rotogravure press, will need several weeks in pre-press to finalize the design with the brand, order the necessary plates or cylinders, and achieve proper registration for the layout and colors. On the other hand, a digital press requires no plates or cylinders and can instantly print any graphics uploaded to its software.
Ink that has been printed on the surface of a flexible package is almost always buried under another layer, a process called finishing, to ensure it does not smudge or rub off. There are several finishing methods that can be used for flexible packaging.
Varnishes and Lacquers: A varnish or lacquer is a viscous substance spread evenly over the print layer to provide it with a clear, thin coating. The most affordable finishing method, lacquers and varnishes provide a relative degree of protection for ink, but they come in limited finishes and may be at risk of rubbing off or degrading over time. They are typically applied using a printing deck on a conventional press.
Thermal Laminates: Thermal laminates include a heat-activated adhesive layer on the back side of the film. Once this adhesive is melted, the laminate is pressed against the package and quickly cures as it cools. This method tends to be pricey at large volumes because the adhesive layer adds cost to the film. However, it enables packaging to be processed further the same day and is available in the widest range of finishes.
Films: Unlike thermal laminates, unsupported films have no adhesive layer, enabling the converter to choose which type of adhesive they use. They are more durable than varnishes or lacquers and more affordable than thermal laminates. Films like those found in the Nobelus unsupported film portfolio can provide unique haptic and visual effects that help packaging stand out.
SHAPING, FILLING, AND SEALING
At this point in the process, the package is typically still a flat web made up of several functional layers and a final print layer (pre-made packaging goes to press after the web has been shaped). To create the packaging that will ultimately sit on the store shelf, the converter has to manipulate the web into a specific shape, insert the product that will be sold, and then seal the finished package to ensure the product is not exposed to the outside world until it is opened by the customer. Some operations focus solely on filling and sealing packages, a function known as co-packing.
Because flexible packaging can take so many different forms, many converters make use of specialized equipment that combines the shaping, filling, and sealing processes. Because there are many different types of equipment, such as stick pack and horizontal form fill and seal (HFFS) machines, this section will use the popular vertical form fill and seal (VFFS) machine as an example. These units can create chip bags, candy wrappers, and a variety of other packaging types. While their exact processes may differ, most flexible packaging equipment performs these same basic functions.
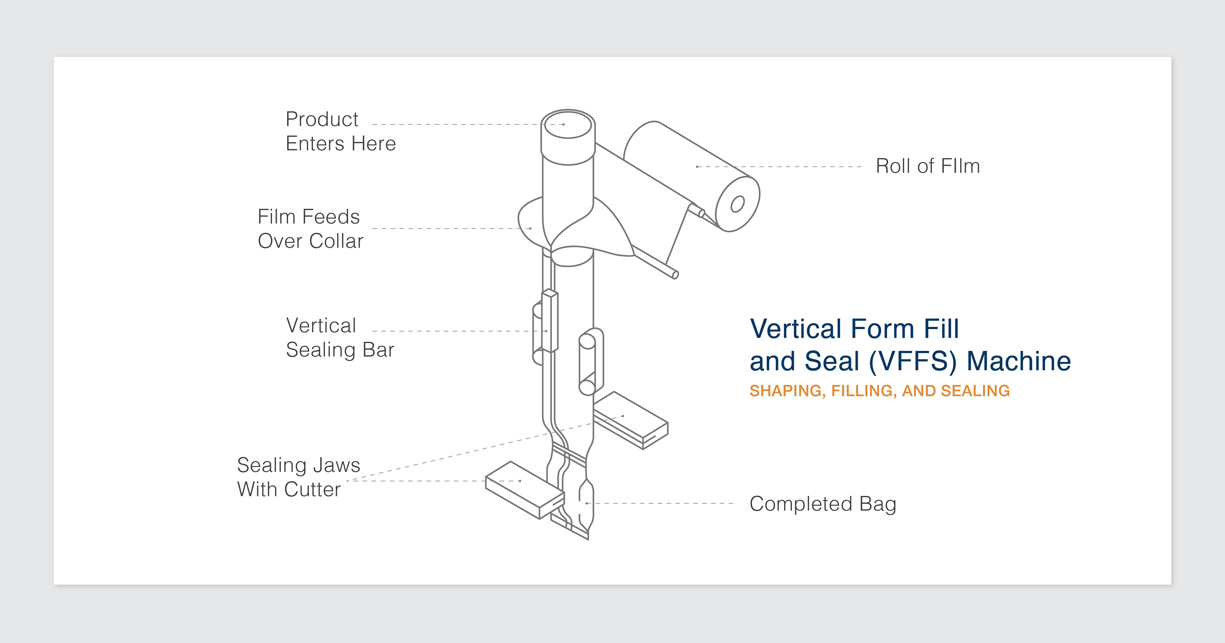
A VFFS unit takes in web via a roll at the top and shapes it around a hollow forming collar. The size of the package is based on the width of the film web and the size of the forming collar used in the run. A vertical sealing bar near the collar ensures the outside edges of the web are bound together using heat, making the web an enclosed tube. As the tube is guided downward, horizontal sealing jaws at the bottom of the unit press the sides of the tube together to seal it off from the material below. Product is funneled through the hollow collar in preset portions and lands against the sealed bottom of the tube. When the process repeats, the seal bars close the top of the bag with the product safely resting inside. The finished bags are then separated at the seal and boxed up for shipping.
WANT TO LEARN MORE?
Whether you’re a new flexible packaging converter who has questions about which materials and processes you should use or a printer who is considering expanding into the flexible packaging industry, our experts and solutions managers are always available to provide consultation. Contact a Nobelus team member today through phone or email for detailed guidance concerning laminates and films, equipment, workflow, processes, and more.