WHAT IS CORONA TREATMENT?
At some point or another, most every printer who has utilized thermal laminates or unsupported films in their finishing process will have seen the words “corona treated” printed on the roll label. Whether they will be used to create brochures, folding cartons, book covers, prime labels, or any other type of print or packaging, the vast majority of films are corona treated before they arrive at the printer’s facility.
In fact, corona treatment is so important to the lamination process that the film extruder, supplier, and even the printer or converter may perform additional treatments at different stages of the product’s life as it is shipped from location to location to ensure its effects do not wear off. But what is corona treatment, and why is it so crucial that laminates and films undergo this process before they are loaded onto a film mandrel?
Understanding Corona Treatment
In simple terms, corona treatment is a process that physically changes the surface of a laminate or film to increase its surface energy. Surface energy, or dyne level, describes the strength of the bonds that exist between individual molecules on the film’s surface. The stronger the bond between molecules, the more hydrophobic (or water repelling) the surface of the film. When these bonds weaken or break, the film’s surface energy increases, and the film becomes more receptive to liquids. When someone talks about a film having a high dyne level, it is just another way of saying that the film’s surface energy has been raised due to these broken molecular bonds.
How Corona Treatment Is Performed
However, this is far from a simple process as untreated polymers naturally maintain strong bonds between molecules, and it takes high amounts of concentrated energy to disrupt the film surface. These high energy levels can be achieved by using an activator, which is powered by a high-voltage, high-frequency generator. When it is time to corona treat a film, a metal electrode channels energy from the generator downward, and the film is pulled through a small gap between the electrode and a silicone-covered aluminum roller. The air in this tiny gap is ionized by the electrode, creating corona discharge, also known as air plasma. As the film passes through this plasma, high-energy electrons are forced into the film’s surface, disrupting the molecular bonds, oxidizing the film surface, and raising its energy levels.
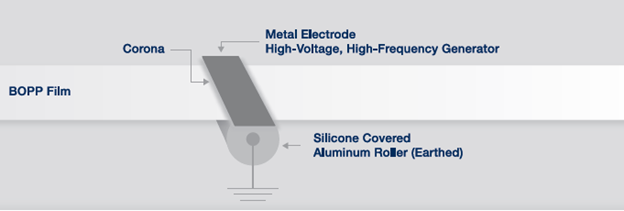
CORONA TREATMENT AND LAMINATION
Now that we know what corona treatment is and how it is performed, we need to understand why it plays such a critical role in the lamination process. As mentioned before, untreated polymer films are naturally hydrophobic, which means liquids do not adhere to them with any reliability or consistency. This poses an issue for the printer or converter as the lamination process hinges on the film layer’s ability to adhere to a variety of viscous substances, such as inks, adhesives, and coatings.
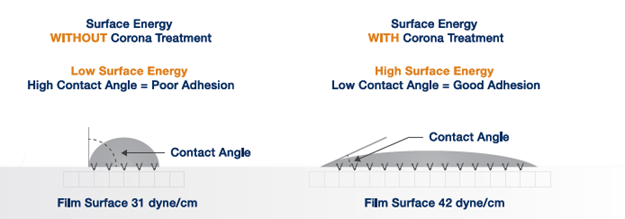
If a film used in a flexible package does not have appropriately high dyne levels, the package will fall apart because the film surface will not be receptive to the adhesive that binds it to the substrate. Likewise, a thermal laminate with low dyne levels will not be receptive to post-laminate processes like spot UV, gluing, or overprinting. When the surface energy of a film is raised through corona treatment, it reduces the contact angle of the liquid, allowing it to spread out over the film’s surface and lie flatter for stronger adhesion. Laminates and films that have these characteristics are described as “wettable.”
FREQUENTLY ASKED QUESTIONS
Corona treatment, surface energy, and wettability are complicated topics for even experienced printers. Sometimes getting an answer to one question can lead to several branching questions. Let’s look at some that naturally come to mind when discussing corona treatment.
When is a film corona treated?
Most films are treated by the film extruder when they are first manufactured to ensure the film is both ready for immediate use and also receptive to future corona treatments. Certain films, such as polypropylene (PP) and polyester (PET) may never be receptive to corona treatment if they are not treated immediately after being extruded, so purchasing pre-treated films is usually preferrable. Over time, the molecules on the film’s surface will return to their original low-energy state, and the benefits of this initial corona treatment will wear off. Other conditions, such as age, material composition, and ambient temperature, can also impact how quickly a specific film’s dyne levels drop.

Typically, enough time has elapsed between the extrusion process and the laminate arriving at the printer’s facility to warrant further corona treatments before the film is used for lamination. If the film is ordered through a laminate supplier or distributor, the seller may perform an additional treatment, called a bump treatment, before the film is shipped to the printer. Many larger printing operations have in-house activators that give laminates a bump treatment in-line immediately before it is applied to the substrate to ensure dyne levels are as high as possible. Because specialized equipment is needed to perform corona treatment, smaller print operations who cannot perform corona treatment in house should always communicate with their laminate supplier to ensure their orders will arrive with the correct dyne levels.
How many times can a film be corona treated?
Although bump treatments can be an excellent way to increase a film’s dyne levels, the film’s surface energy cannot be raised indefinitely. Much like how a battery can only hold a set amount of energy even if it is left to charge for prolonged periods, each film material has a limit regarding how much surface energy it can hold, with biaxially oriented polypropylene (BOPP) and high-density polyethylene (HDPE) holding the most energy among standard film types.
Continuing to treat a film that has already reached its maximum dyne level will not have any effect beyond potentially damaging the surface of the film and making the roll unusable. For this reason, printers should be very cautious when deciding which laminate will be best for their application. Having a proper understanding of the properties and limitations of each film is a crucial step in consistently creating high-quality, high-performing laminated prints and packaging.
How do you test a film’s dyne levels?
Printers should always test the dyne levels of any laminate or film they receive into their facility to personally verify that it meets minimum requirements for their job.While the film extruder and supplier bear some responsibility for accurately communicating the dyne levels of any products they sell, it is ultimately the printer whose workflow, revenue, and reputation are most at stake. Additionally, an initially accurate dyne level measurement may change over time if the film is shipped and/or kept in storage.
To test a film’s dyne levels, purchase a set of dyne pens or markers. Each pen will be labeled to denote which dyne level it is measuring for. Starting with a pen near your desired dyne level, press down on the film surface and drag the marker across. If no beading occurs within several seconds of the ink being applied, move up to a higher pen number and repeat the process, moving up one dyne level each time. Once significant beading is apparent within 2 seconds of ink placement, you have successfully found the dyne level of the film. The dyne level of the film is the highest pen number where the ink remained consistent for the full 2-second testing period.
REACH OUT TO LEARN MORE
Nobelus understands that print finishing is a complicated process filled with outliers and exceptions. If you feel like your questions weren’t answered by our article, be sure to reach out via phone or email. We have a team of in-house experts who can share knowledge on everything from the chemistry of corona treatment to how the process affects real-life applications, embellishments, and post-laminate processes. Our solutions managers are always eager to answer questions and work with you to find the right materials and equipment for your unique operational needs.