THE IMPORTANCE OF PROPER FILM ROLL CARE
Many different steps, supplies, and processes have to meld together flawlessly to produce a high-quality printed piece. Finding the right press, making sure colors are accurate, ensuring the laminating process yields a smooth, wrinkle-free sheet – printers have to take a huge number of factors into account to turn a blank piece of paper into a carefully crafted product that perfectly serves a customer’s needs. Amid all these factors, it can be easy to overlook the importance of how rolls of laminates or films are handled and stored before they are put on the laminating system.
However, improper storage and treatment of a film roll can result in poor-quality prints, expensive replacement rolls, and much frustration for operating staff and owners alike. To ensure even the newest printer has a solid knowledge of how to handle film rolls, we will go over some basic things any printer should know when it comes to keeping laminates and films in peak condition in their facility.
KEY CONSIDERATIONS
While the average printer will likely continue to perfect his or her laminate roll storage and handling systems over the years as they gain experience, there are a few rules of thumb that should be followed from the start. The ultimate goal of each guideline is to make sure each laminate roll is ready to be loaded onto the film mandrel and produce perfect prints at a moment’s notice.
1. Prepare the Right Equipment and Storage Procedures
A broad number of things can happen to film rolls between the time they are offloaded from a truck and when they are put onto a film mandrel. Some factors can damage the integrity of the roll and require it to be replaced, while others may affect the quality of the completed laminating job.
Keep laminate rolls clean by storing them in bags. OPP and PET films can be stored in plastic bags, but some material types will need metalized bags. While it is best practice to make sure your warehouse or other storage area is kept generally clean, dirt, grease, and bugs can be an issue in even the cleanest and most well-kept space. This practice is especially important for thermal laminate rolls with either a tactile coating or an exposed EVA adhesive layer as the surface could be a bit tacky, even if it is subtle enough to go unnoticed by touch. You may also find that the ends of a roll are more likely to gather dust and other contaminants as a bit of adhesive will be exposed regardless of how the roll is wound. If you see that your laminate roll has accumulated debris, unwind the outermost layer of the roll and discard it immediately before lamination. This should prevent dirt specks and other tiny imperfections from ruining the first set of laminated sheets.
Never place film rolls directly on the floor. This practice is important for two reasons.
- Corona-treated films actually run the risk of losing their improved surface energy when placed on concrete. Corona treatment involves channeling electrons into the surface of a film to increase its surface energy, but concrete will ground the film roll, giving the electrons a way to leave the film and draining the surface of its energy. To slow the rate at which corona-treated films return to their original dyne levels, elevate them above concrete flooring using a wooden pallet.
- Rolls stored on the floor may be accidentally kicked, torn, or moved as personnel on the production floor go about their tasks. Keeping film rolls organized on pallets or rods will help keep them out of the way in addition to removing a tripping hazard.
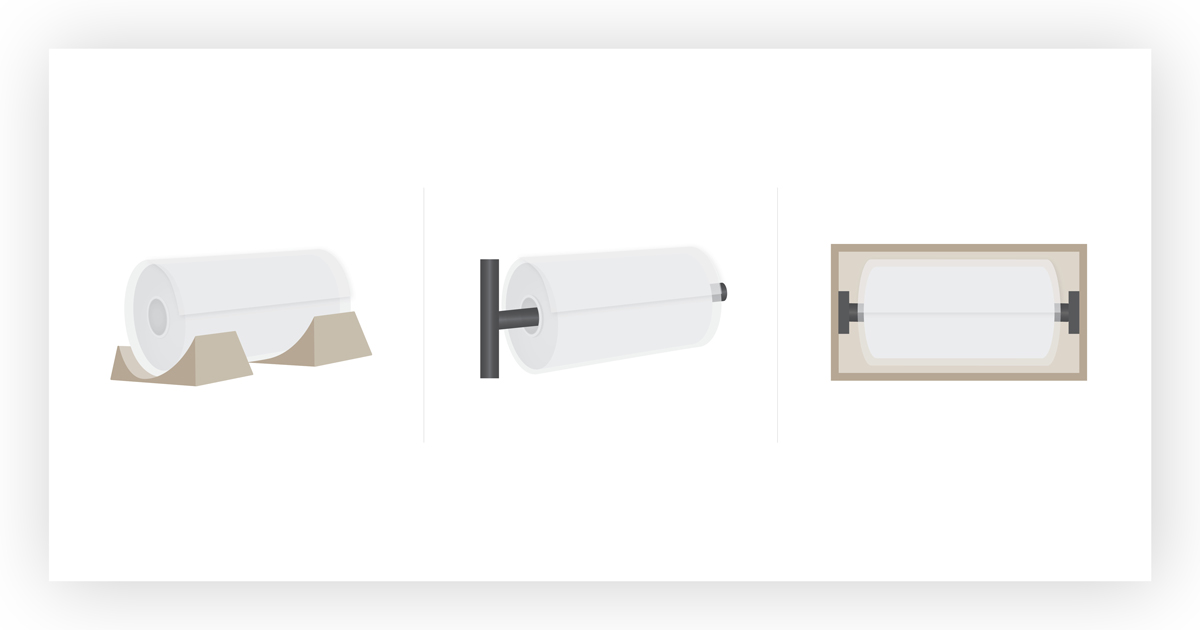
Use common sense when handling film rolls to prevent them from becoming damaged. Laminates and films are often incredibly thin and therefore prone to tearing, puncturing, and wrinkling if they are not handled with the utmost care. Never place a film roll on a rough surface, even if the roll is being set down briefly, and avoid “walking” rolls on their ends to move them around. Instead, move rolls by carrying them until they can be set down somewhere safe. For some laminate rolls, this may mean that multiple staff members have to work together. Larger rolls may require the use of a roll lift to move them safely; take extra care not to overburden employees and risk harm to materials or people.
Store film rolls in the right environmental conditions for best results. Laminate and film rolls should always be kept indoors and out of direct sunlight to ensure they stay at a moderate temperature. Storage facilities and warehouses that hold film rolls should be temperature and humidity controlled to prevent the quality of the film from being negatively impacted over time.
Check the quality of the film rolls that enter the facility. While Nobleus takes extra care to slit and ship only high-quality rolls, materials obtained from other suppliers may at times be wound too loose. In these instances, the roll will display a telescoping effect as it unwinds across itself. These rolls are very difficult to move and can create issues in lamination quality.Always verify that the film rolls accepted into your facility are acceptable for storage and eventual use.
2. Understand the Film Material
Certain materials have storage and handling requirements that extend past the general rules of thumb listed above. We cannot cover every material type in this post, but we will look at a couple of examples to show why material types can make a big difference in storage conditions.
Nylon is a film material valued for its hygroscopic properties, which means it allows moisture and humidity in the environment to pass through it without affecting the film. For this reason, nylon laminates and films are frequently used in applications that should keep their shape after repeated use and handling, such as softbound book covers that need to lie flat against the book pages even after a day at the beach.
To ensure nylon retains these lie-flat properties, it must be stored in a metalized bag when not in use. A printer who is unfamiliar with this special requirement might be frustrated to find that their roll is wrinkling and forming lines as nylon wicks away moisture in roll form. Fortunately, the roll may be salvageable if the damaged outer layers are removed, although this depends on the exposure conditions.
Like nylon, cellulose (CLS) is also moisture sensitive and must be stored in a metalized bag. It is prized for its eco-friendly construction and easy tear properties in a variety of applications. However, these same positive qualities mean that this material has even more handling requirements due to its brittle, fragile nature. In addition to all of the rules laid out in the previous section, cellulose rolls should be treated with the utmost care to prevent nicks or tears that could cause web breaks in the film.
Cellulose rolls should be carried by inserting a mandrel through the core with adequate support on each end to ensure the roll is not dropped. These mandrels should not be hammered into the core to prevent damage to the roll’s edges. A roll lift with wheels can also be used to transport cellulose films.
Other material types and finishes often have their own similarly complex storage requirements, so printers should always make sure to inquire about new products to make sure they are keeping them in the correct handling and storage conditions.
3. Organize and Label Each Roll
When prioritizing handling and storage conditions, it can be easy to overlook organization and labeling, but these practices are crucial to eliminating confusion down the line and creating a smooth workflow.
Always make sure each film roll in the facility is properly labeled with its product number and any basic descriptors operators may need to identify it. It should also be readily apparent whether the film is wound adhesive in or adhesive out. If a material is mapped and matched, it should always be labeled North or South accordingly to prevent mismatched films from causing curl in a finished piece.
Fortunately for the printer, most laminate and film suppliers, including Nobelus, will diligently label each film roll that leaves their facility to facilitate storage for their customers.
4. Rotate Your Inventory
Always be sure to use up older film rolls before opening a newer roll in a first-in, first-out system. Over time, corona-treated rolls will naturally lose their surface energy and return to their original dyne levels. While certain facilities may have the ability to perform a bump treatment on a film before it is put on the laminator, the most efficient, cost-effective way to preserve the dyne levels of film rolls and ensure high-quality laminating results is to keep inventories rotated and proactively avoid the issue.
Even operations that utilize a first-in, first-out system should make sure to dyne test older films before running them on live jobs to verify that they can achieve a proper bond. Be thoughtful about how much film is ordered at once or kept in stock to streamline the lamination process and reduce the likelihood of poor bond strength on finished jobs.
5. Be Aware of Safety Concerns
Finally, do not overlook the importance of operator and staff safety when storing and handling film rolls. Always verify that the staff tasked with moving film rolls have proper equipment or adequate manpower to complete the task safely and without undue strain.
While most film rolls can stand on their ends without being damaged, large, wide-format rolls should generally be stored in a horizontal position as they can topple over and harm other rolls or people in the vicinity. If space is an issue, film rolls can be stacked on top of each other on pallets so long as they are fitted with core plugs that keep them in place and keep them from falling over.
Even with the use of core plugs, inventory management should exercise caution and common sense when deciding how high to stack the rolls. No storage system is worth the risk of injuring an employee.
NEED MORE INFORMATION?
If you have more questions about any of the topics covered in this article or want to discuss something we didn’t go over, we welcome you to reach out by phone or email. The Nobelus team is always eager to hear about your unique operational needs and help find the solutions that work best for you. Our product development managers and quality control experts have years of experience dealing with all types of laminates and films and can address any questions or concerns you have about how to care for Nobelus products.